The Plantims Tech LIMS module, responsible for overseeing and scheduling all processes within an industrial laboratory, has been developed and deployed in accordance with ISO 17025 standards. To ensure user-friendly utilization of the LIMS module, the software interface has been designed to closely resemble the Windows 11 operating system, simplifying user interaction with the desired software
The module in question boasts diverse infrastructures and extensive functionalities, outlined primarily as follows:
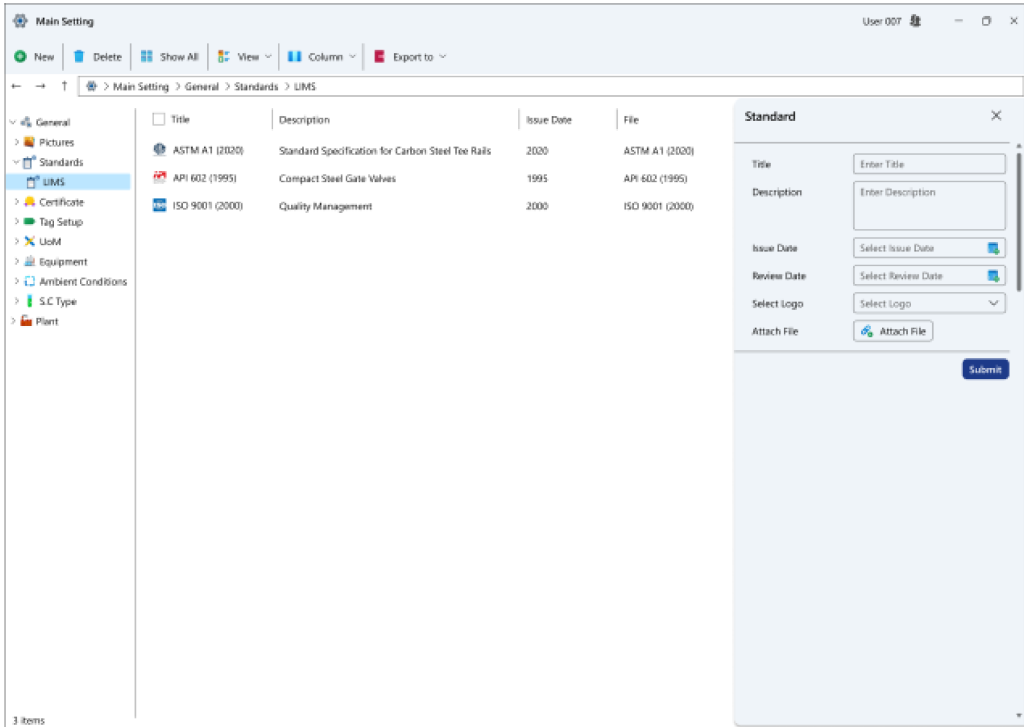
Initial Configuration
In this segment, all fundamental data pertinent to an industrial environment such as a refinery is logged into the system. This includes essential information such as:
- Tag categorization details: Tags within this system can display various categories.
- Sub-tag particulars: Tags are subdivided into distinct subcategories within this system.
- Tag classification specifics: Tags are segregated into different types within this system, each accompanied by user-specific descriptions.
- Tag suffix insights: In addition to type, tags within this system also possess recognized suffixes, which can be defined herein.
- Refinery particulars: The system is structured to manage information related to multiple industrial sites cohesively.
- Zone specifics: Each industrial site can be further subdivided into smaller zones within this system.
- Unit details: Various units for diverse operations exist within each industrial site, all of which can be defined within this section.
- Train/Phase/Package data: Each unit within this system can be further compartmentalized into smaller categories known as Train, Phase, or Package for refinement.
- Tag insights: Information regarding different tag types can be registered within this system based on predefined classifications. Each tag has the potential to harbor multiple sub-tags. For instance, sample collection zone tags, each housing a list of applicable analyses that can be performed on the respective sample.
- Standard specifics: The laboratory system segments within this system adhere to ISO 17025 standards. A pivotal aspect addressed in this standard involves specifying the analysis methodology, which can be registered herein. Furthermore, in the laboratory test definition section, the applicable standard can be selected for various tags. According to standard 17025, each standard must undergo periodic review, with the latest version of said standard uploaded onto the system. Additionally, the complete list of review timelines alongside the uploaded file can be accessed within this system.
- Certificate category details: Various certificate types may be requisite for conducting diverse analyses, necessitating acquisition by personnel. Within this section, various certificate types can be registered, and personnel who have obtained said certificates can be delineated.
- Measurement unit particulars: Various measurement units can be defined within this section, each accompanied by distinct symbols. It’s noteworthy that the measurement unit type can be selected within the tag definition section.
- Safety equipment insights: Various safety equipment essential for sampling or analysis can be registered within this system.
- Cylinder type specifics: Information pertaining to various cylinder types potentially present at an industrial site can be logged within this system.
- Manufacturer plant particulars: This system allows for the registration of information concerning manufacturer plants and supplier companies. Additionally, it enables the identification of which plants (brands) each supplier provides.
- Laboratory environmental conditions: As per standard 17025, laboratory environmental conditions must be recorded during each analysis. Therefore, this section has been established within the system to document the various environmental conditions necessitating recording by personnel.
- Sample collection zone types: Within this section, various sample collection zone types can be registered.
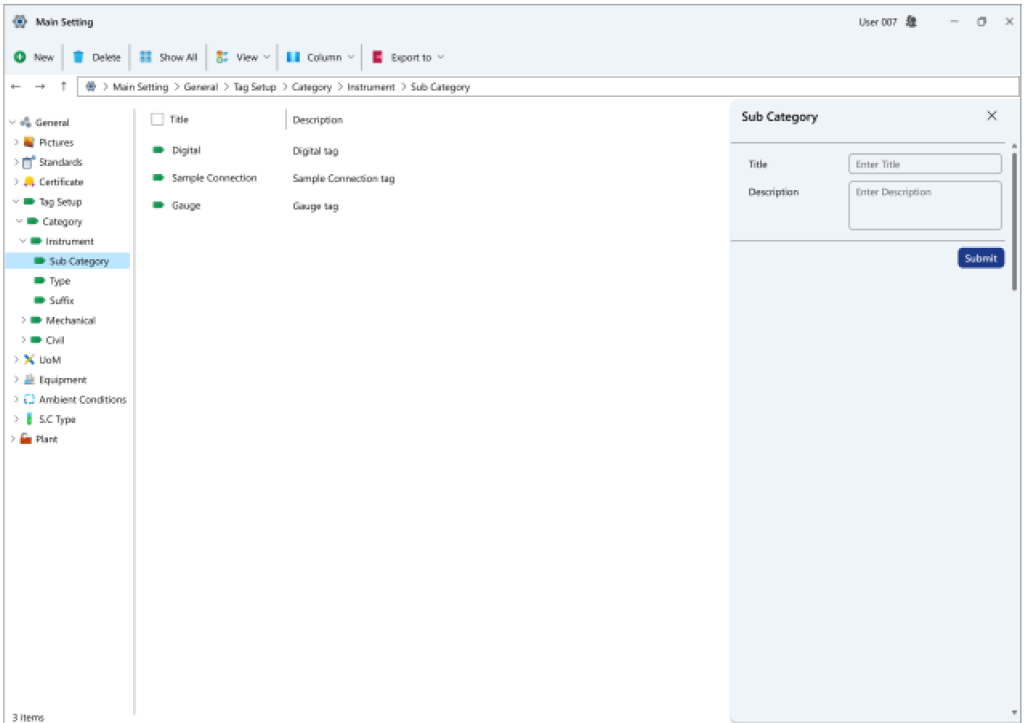
Report Management:
Within the report management section, efforts have been made to optimize functionality and features with minimal page navigation, ensuring users of this module can swiftly access the necessary tools. Among the key features are:
- Dashboard: Users can customize and save pages based on specific laboratory tags, facilitating rapid access to information and charts for those tags during subsequent visits.
- Creation and viewing of diverse reports: Users can generate various reports tailored to their needs and view them in their preferred historical formats, whether in charts or tables. Additionally, outputs in Excel and PDF formats can be extracted.
- Daily results table view: Users have the option to view data entry results for each selected day in table format.
- Formulation of computational formulas: Users can devise formulas for virtual tags using other real or virtual tags.
- Material consumption tracking for each tag: Users can specify the quantity of materials consumed from the inventory for each specific tag during the relevant analysis.
- Creation of routine sampling schedules: This module allows users to plan sampling schedules at various intervals, such as daily, bi-daily, weekly, monthly, annually, or at the start and end of each month.
- Recording of routine laboratory and operational tag information: Users can log information pertaining to the results of various tags.
- Automatic calculation of formulas and result registration: Predefined formulas are automatically computed upon registering results for dependent tags.
- Recording of non-routine requests: In addition to routine planning, users can submit non-routine requests for sampling and result registration for various tags. These requests follow a predefined process, starting with approval or rejection by the unit manager. If rejected, the user must provide relevant explanations for necessary corrections or resubmission. Subsequently, the laboratory supervisor approves or rejects the request, mirroring the approval stages by the manager. Once approved by the laboratory supervisor, the sample is added to the laboratory task list for sampling and result registration.
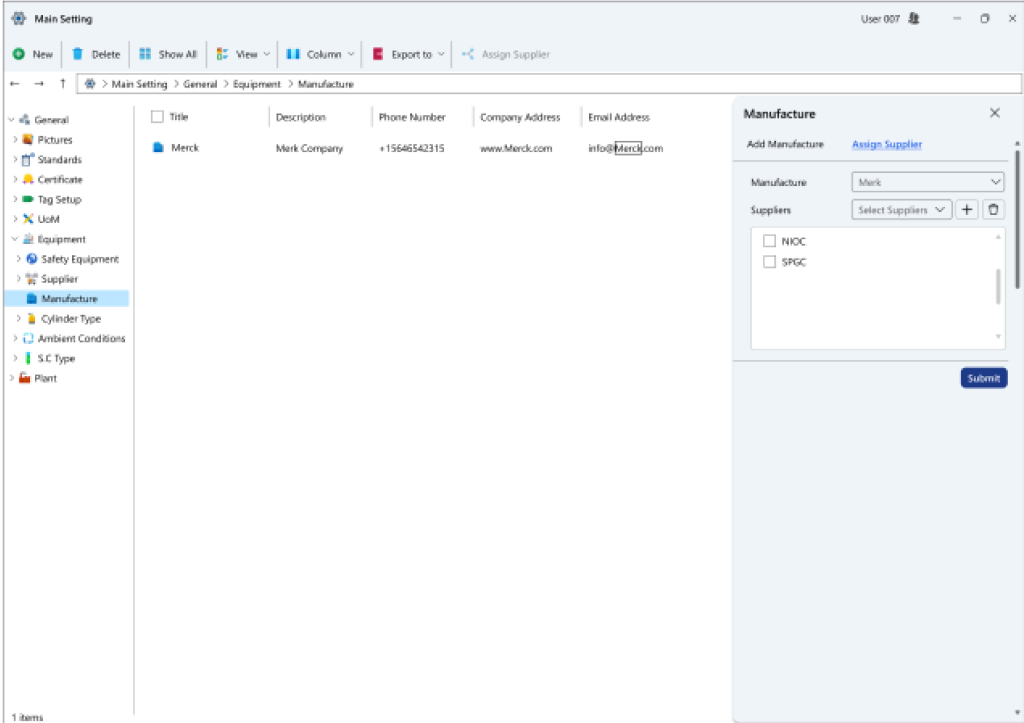
Laboratory Inventory Management
Within this segment, all procedures concerning the inflow and outflow of goods into the inventory are documented, offering a comprehensive report on inventory levels based on expiry dates. Furthermore, it allows for the recording of equipment information utilized on the industrial site for periodic and daily validation processes.
- Recording Material Details: Various material types and diverse components housed within the inventory are logged within this section.
- Cataloging Gas Cylinder Information: Under the initial configuration, details regarding different cylinder types alongside their specific specifications are entered. This facilitates the registration of diverse cylinders existing at an industrial site, along with updating their respective statuses. Moreover, a suitable scheduling mechanism is established for reviewing cylinder statuses, prompting necessary user action when required to document potential changes in cylinder status at designated intervals.
- Equipment Recording: Within this segment, particulars regarding the apparatus employed at the industrial premises are documented. This encompasses details such as the calibration interval, essential for issuing alerts, and presenting the pertinent form for each device. Another aspect includes the duration for short-term or daily validations. If the calibration period is predetermined, the system will prompt the necessary alert and pertinent form for recording device status and explanations to the user. Furthermore, diverse queries can be predefined for each device, necessitating responses during periodic calibration tasks, alongside completing files and additional clarifications. Additionally, it can be preset that each device may require specific spare parts from the inventory for replacement during calibration procedures, a task also executable by the user during calibration.
- Stock Ingress and Egress Transactions: This division facilitates the registration of inbound inventory transactions as either invoices or non-invoice records, specifying the quantity of incoming materials or components in a record with an assigned expiration date. Similarly, for outbound transactions, an exit record for materials or components bearing a designated expiration date is logged.
- Exhaustive Inventory Overview: In this section, a comprehensive view of each item or component’s quantity is available, either in aggregate or segmented by expiration dates. Moreover, the cardex provides a complete history of all incoming and outgoing transactions for each inventory item.
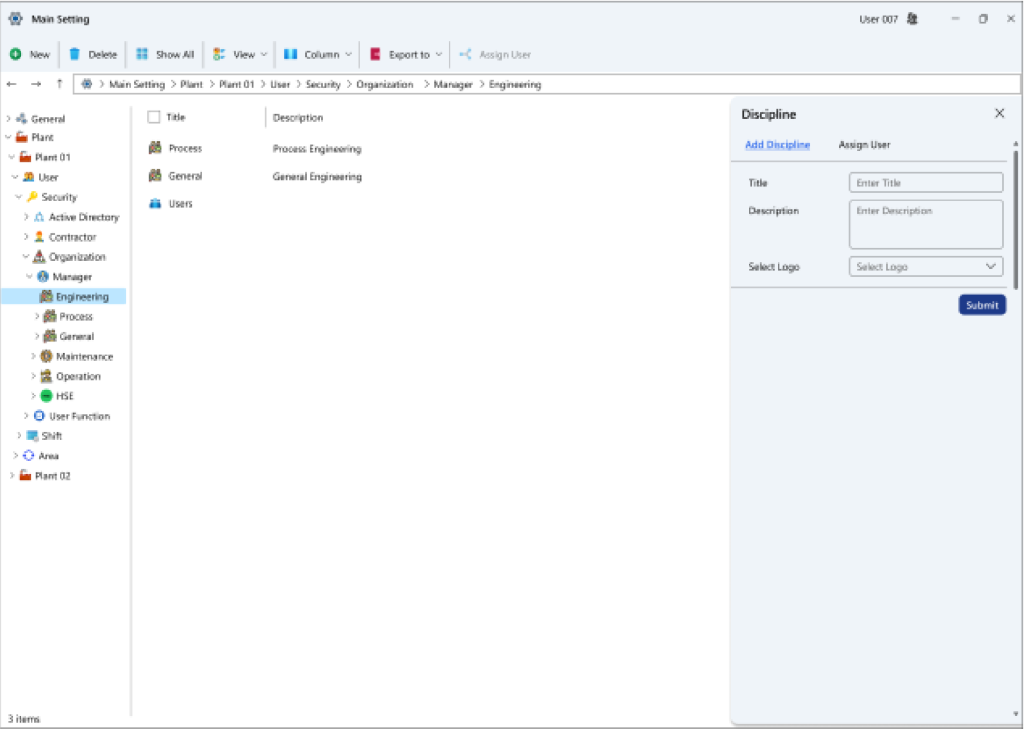
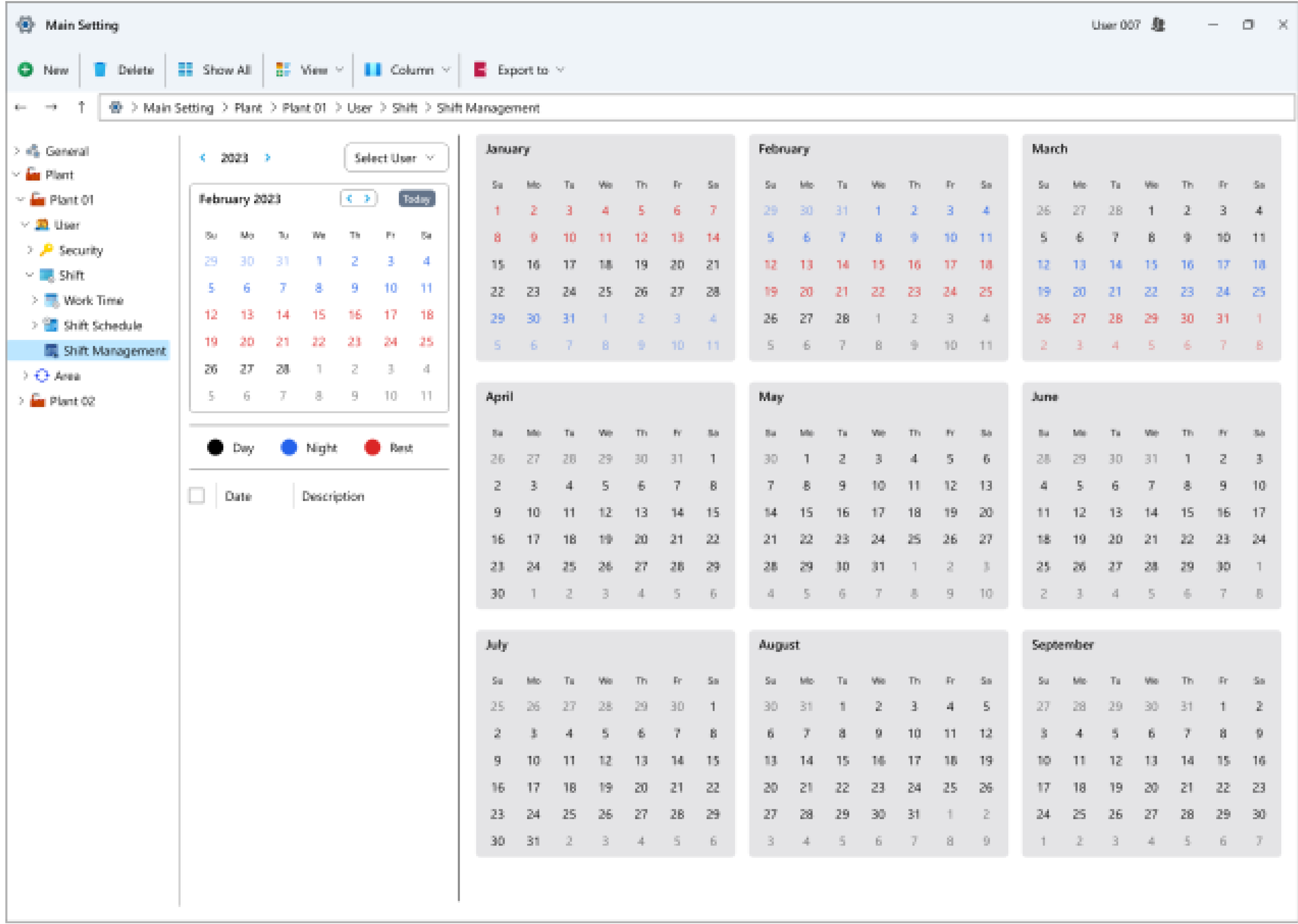
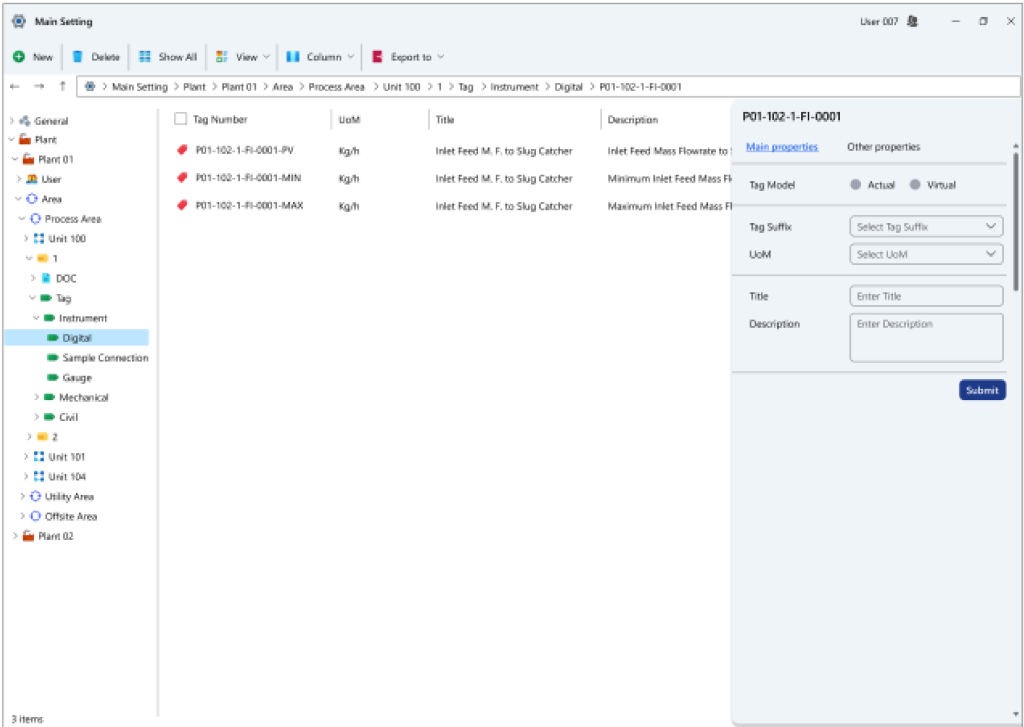
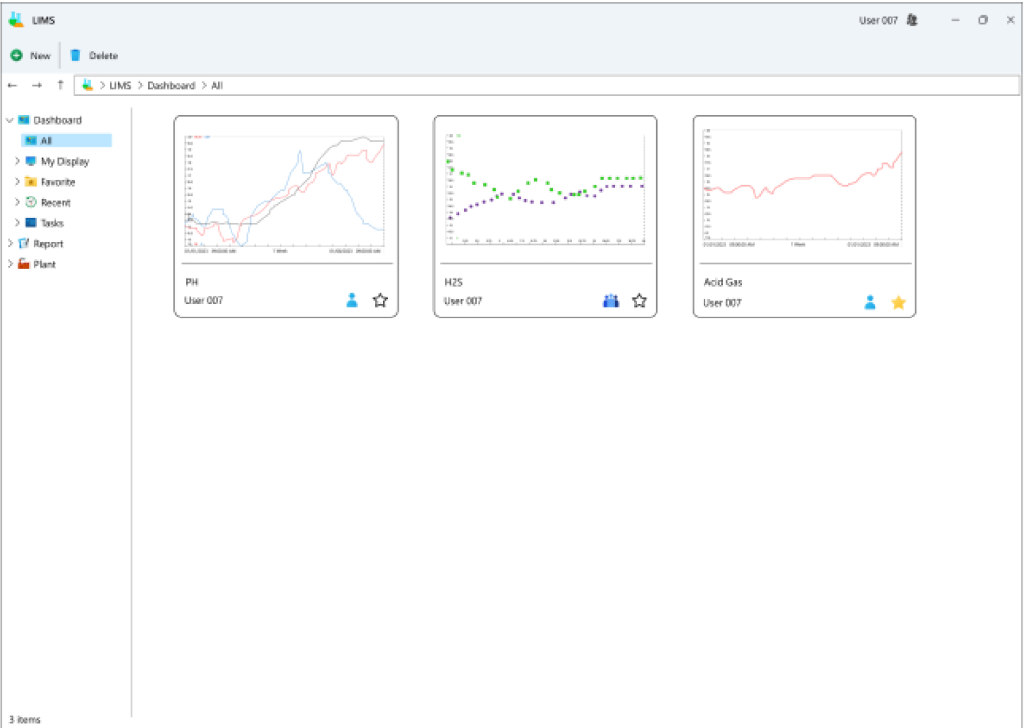
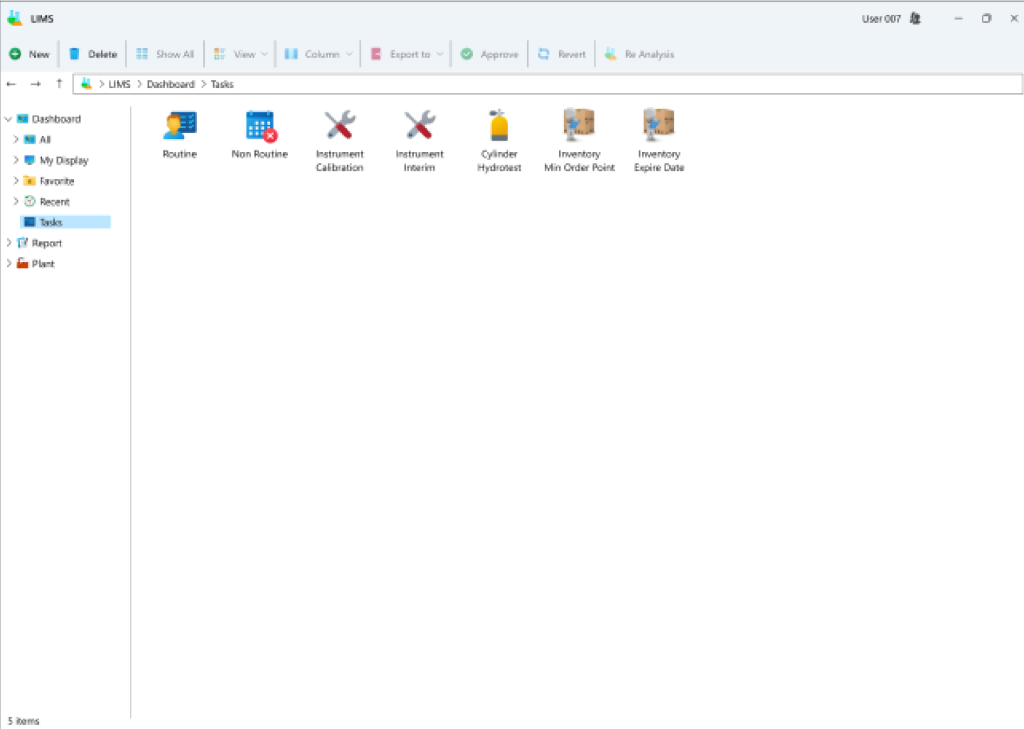
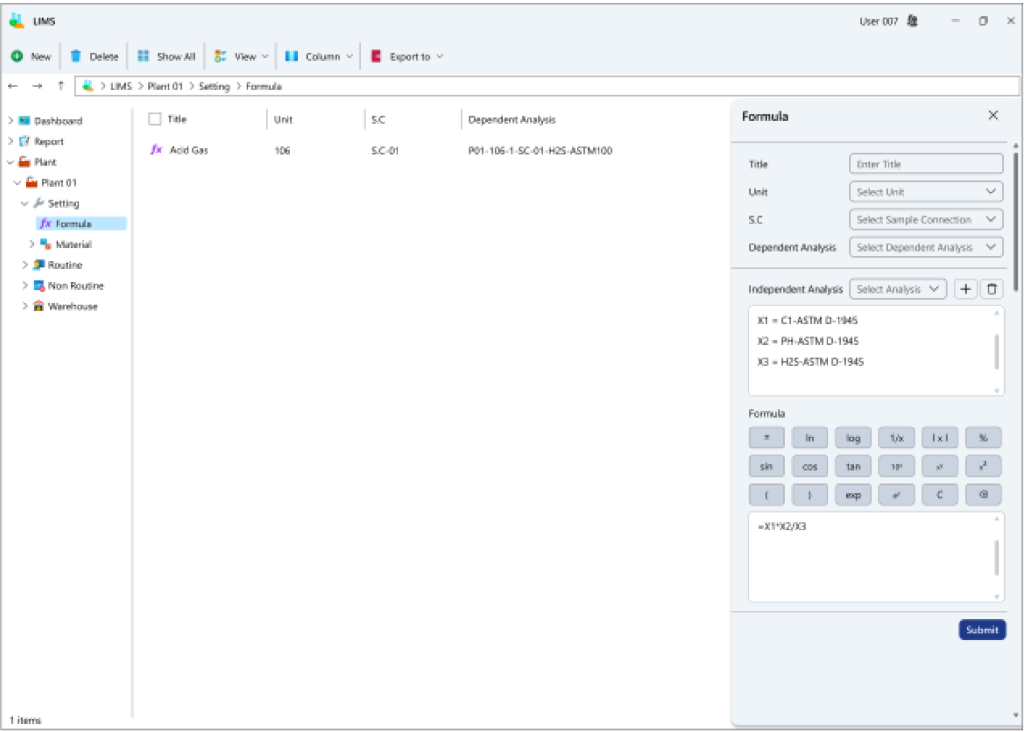
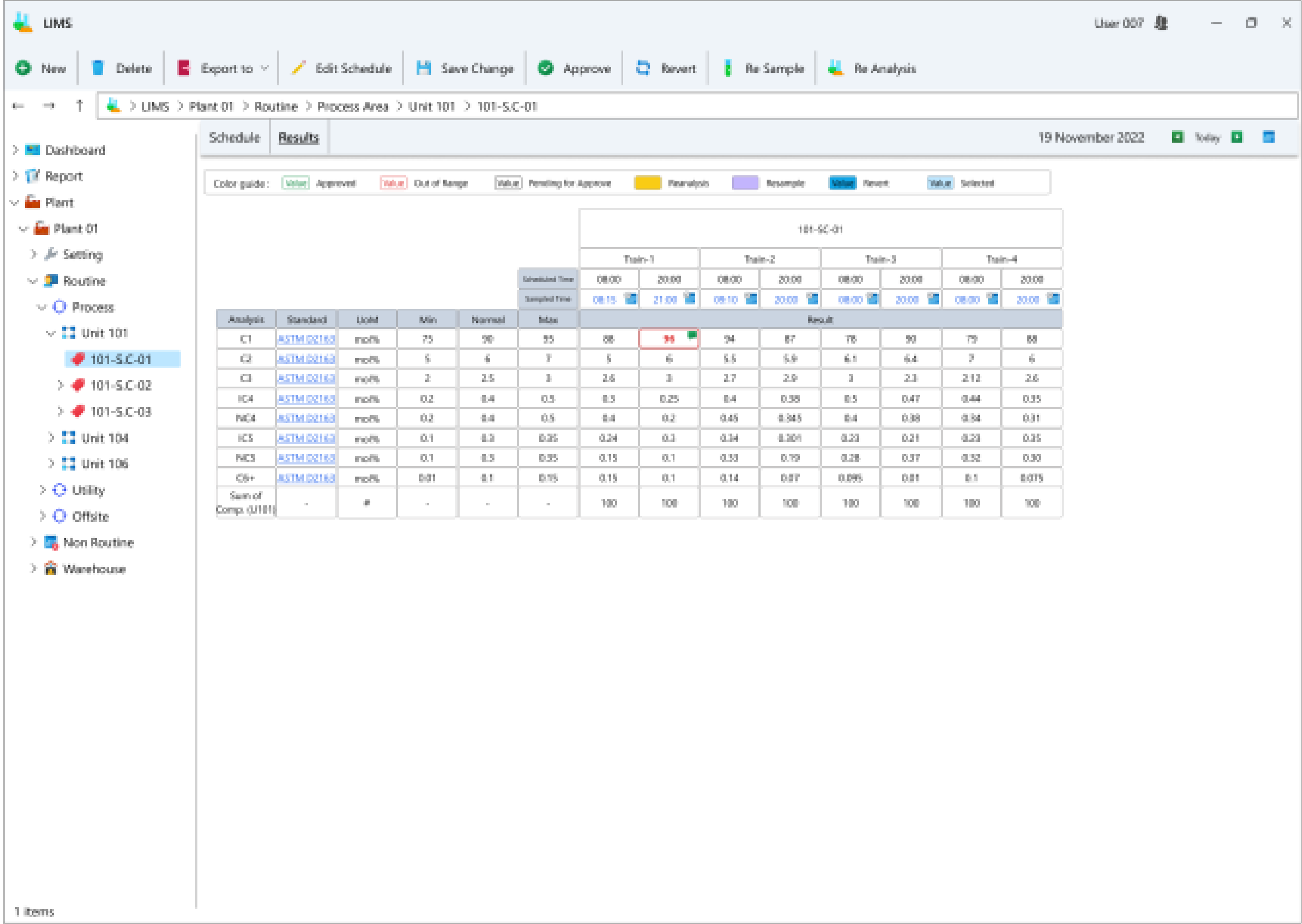
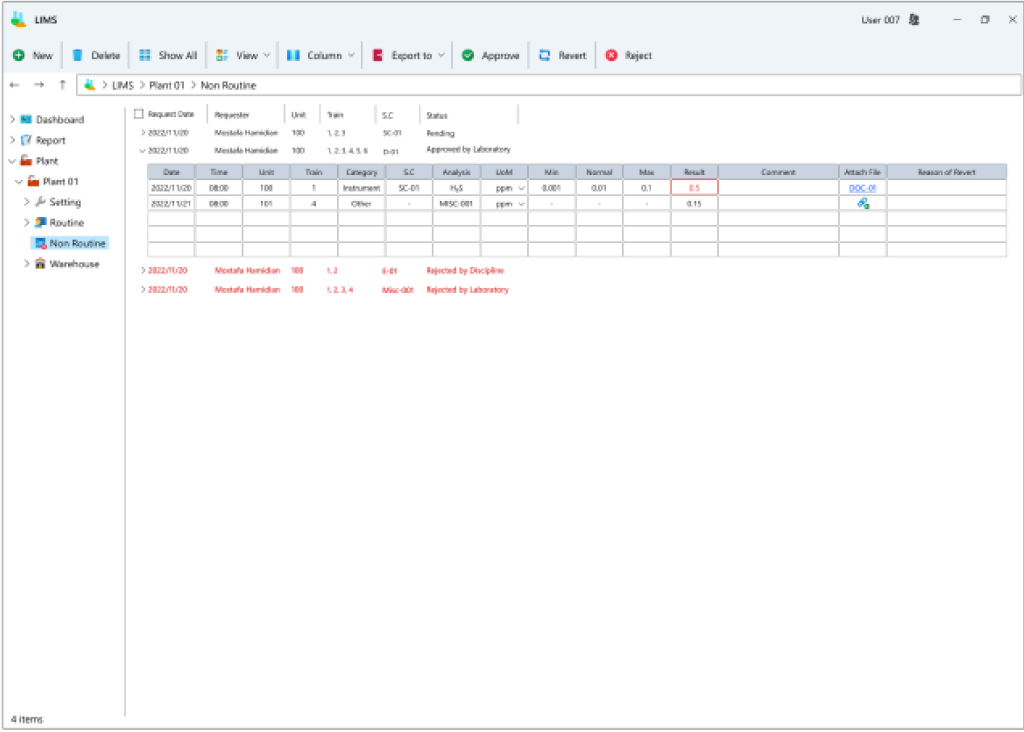
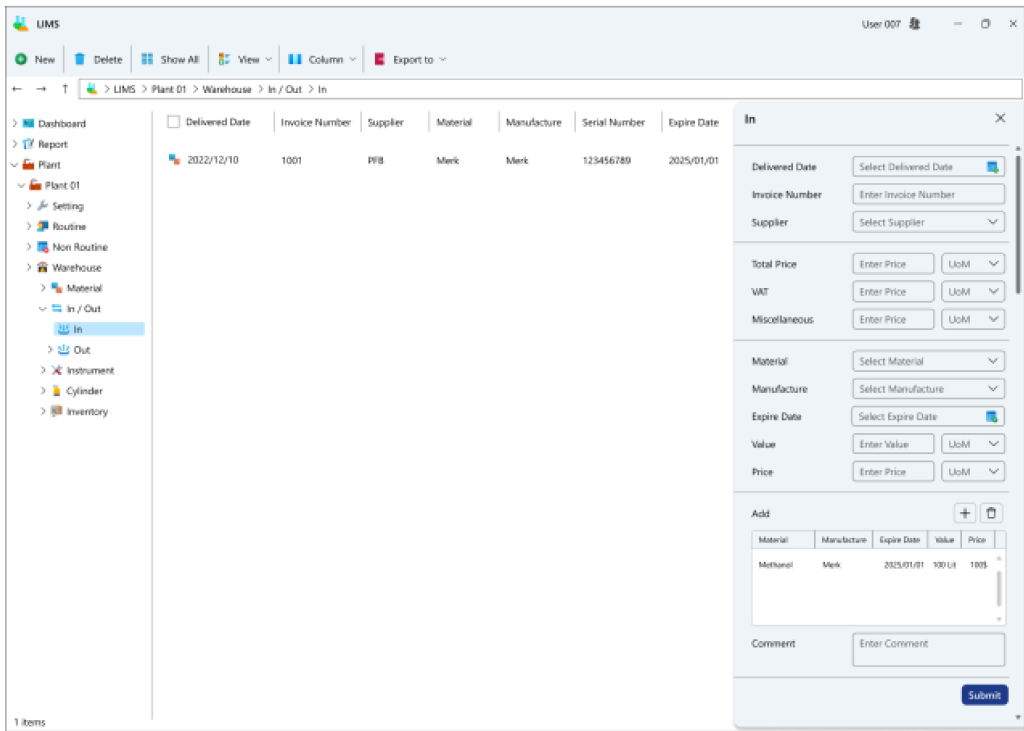
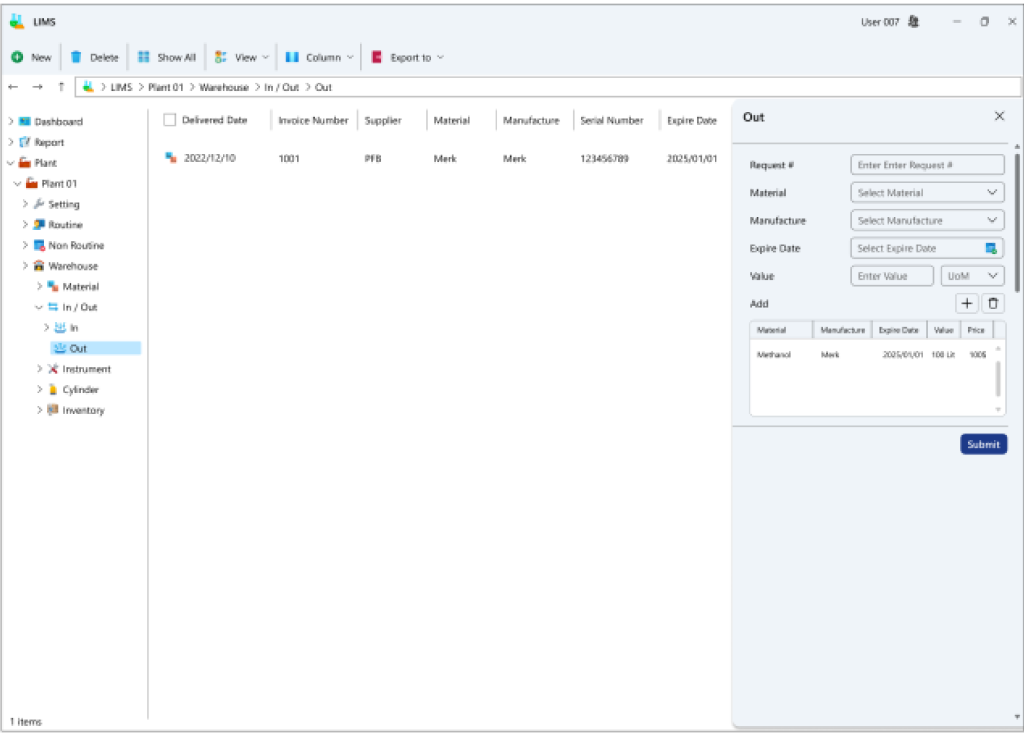
